例行保養: Preventive Maintenance
為了消除設備失效和非計劃性生產中斷的原因而策劃的定期活動(基於時間的周期性檢驗和檢修),它是製造過程設計的一項輸出。
預測保養: Predictive Maintenance
預測保養維修的目的在於評估最佳的保養頻度,尤其著重在運用統計的方式來預測。例如收集過去一年設備故障的頻度以及設備保養的週期,透過數據分析與統計方法 (例如迴歸分析)來訂定最佳(Optimized)保養頻率。
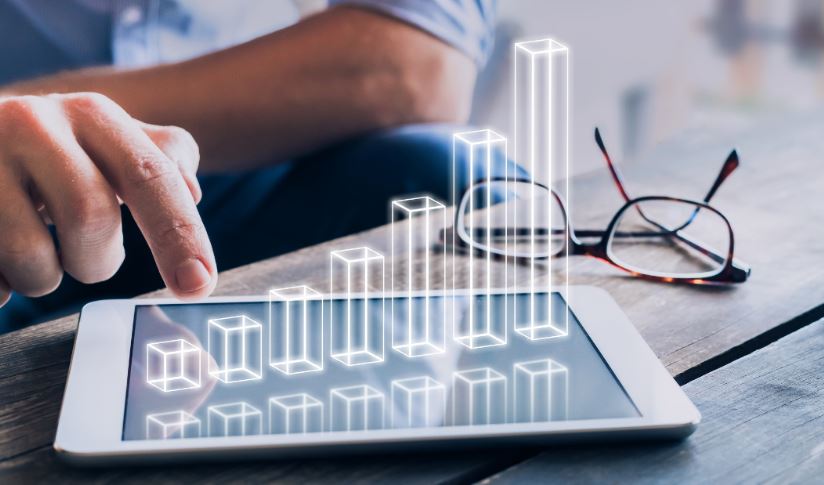
過去工廠在進行例行性的機台設備保養作業時,多以人工巡檢的方式,並倚靠「老師傅」或是供應商的經驗逐一針對設備進行全面的「健康檢查」,然而此種執行方式仍有諸多困難點。
設備監控就是預測保養的第一步 設備監控 選擇3大重點
首先,因勞動力下滑造成人力有限會影響檢測頻率而使執行效率變低;其次,面對眾多且複雜的設備,新進技術人員倘若經驗不足,則容易影響檢測結果,甚至某些場域的環境條件有高度危險性,可能存在工安意外的隱憂。再者,採用定期保養的方式也較難以實時掌握設備的使用情況,尤其對於精密且昂貴的設備而言。
智慧製造專屬4G 工業物聯網平台Android 終端裝置在日本大受歡迎
1次非預期停機,平均停機時間為4小時,損失超過200萬美元
GE Digital針對非預期停機所做的一項全球調查顯示,70%的公司對於何時該進行設備的維護、升級或維修缺乏完整概念。多數公司表示過去3年曾發生至少1次非預期停機,平均停機時間為4小時,損失超過200萬美元
這可能會面臨兩種情況,一種是設備使用壽命還未到極限卻提早進行更換,而若是汰換較為昂貴的設備則徒增營運成本;另一種情況則是,設備尚未到達檢修或汰換的時機,卻已出現異常而不自知,如此所造成的後果更加致命。
導入設備監控系統
倘若設備在異常或超出容許範圍的情況下仍持續進行產線運作,則該產線所生產的產品其良率也會跟著下降,且若無法即早發現設備異常,仍持續運作,不但面臨意外異常停機風險,恐進一步造成周邊零組件跟著損壞或是順帶被打壞( 例如 : 動力皮帶)甚至作業人員工傷,因而擴大故障範圍,拖長停機時間,可謂得不償失。面對這些令人頭痛的問題,癥結在於無法如實、 即時掌握設備的狀態,傳統的例行性維護方式更難以達到此需求,而導入設備監控系統便是能讓業者化被動為主動的關鍵。透過設備監控系統,業者便能改以機器取代人力、以科學方法取代經驗來協助工廠強化機台設備在維修以及預知預防保養的能力。
OT 到 IT
整個設備監控系統最具有價值的部分,在於能夠透過設備運作時所產生的物理訊息了解實時的作業狀態與使用週期,但這些設備所產生的數據資訊不但複雜且具有高度專業性,非一般工廠IT人員可獨立處理,因此,建置sensors,設備監控系統重要的一塊拼圖,便需要由精通各種機台的現場專家(或稱為設備專家)來補齊。
工業物聯網的最大挑戰 就是OT人要懂 IT
工業4.0時代由於資料專家與統計與AI興起,預測保養方興未艾, 可通過運用各種手段進行數據和信號的採集(可以是間斷地採集,也可以是連續地採集)、分析和判斷設備的劣化趨勢、故障部位、原因並預測變化發展、提出防範措施,防止和控制可能的故障出現。
企業採用工業物聯網最在意什麼? 安全性、系統整合與投報率
預測保養 遠遠強過例行保養
美國聯邦能源管理計劃 (FEMP) 所進行的研究估計,一個正常發揮作用的預測性維護計劃與預防性維護相比,可提供 30 % 到 40 % 的節約。據有關統計數據,平均來看,開展一項工業預測性維護計劃可帶來以下方面節約:
- 投資回報:10 倍
- 維護成本降低:25 % 至 30 %
- 故障消除:70 % 至 75 %
- 停產時間縮短:35 % 至 45 %
- 產量增加:20 % 至 25 %
因此許多人大多認為 預測保養是工業物聯網應用成癮的第一步?
智慧製造 工業物聯網的預測保養 遠遠強過例行保養 設備監控時代來臨 有 “ 2 則迴響 ”